Enablers, Barriers, and Critical Success Factors for Effective Adoption of Color-Jet 3D Printing Technology
Abstract
Color-jet 3D printing (CJP) technology-based machines are now being developed, and there is a need to identify the successful adoption of this technology for additive manufacturing (AM). Extensive literature review complemented with experts’ advice utilized systematically helped in the identification of 12 critical factors for the effective adoption of color-jet printing technology. A hierarchical structural model is developed using interpretive structural modeling (ISM) and analyzed using Matriced Impacts Croise’s Multiplication Appliquée a UN Classement (MICMAC). Identified software and the machine cost are primary drivers for this color-jet 3D printing machines (technology). The value of this technology is to provide the product at a lower cost and give useful applications in the area of medical, engineering and concept building. There is a need for developing better quality core material and post-processing material, further supported by enabling machine hardware and software. Accuracy and color texture of the part produced are essential to provide a technological advantage over existing technologies. Post-processing assists in a big way in imparting necessary properties to the part produced. Presently, the infiltrate/post-processing materials are limited, and for large-scale acceptability, one needs extensive multidisciplinary research and development. This research provides a structural model toward the adoption of color-jet 3D printing technology, which can also help users in evaluating this technology in broader AM framework.
1. Introduction
Additive manufacturing (AM) encompasses dedicated technique and technologies to build a three-dimensional solid object, and this process seems to be quite different from subtractive manufacturing. Industries in different sectors are using this technology to describe a process for rapidly creating a part before the final product release. It helps to create an intricate design, which can be manufactured quickly to give a useful final product (Gibson et al., 2010; Bastola et al., 2018; Nsengimana et al., 2019).
Color-jet 3D printing is a part of AM technology being used for automated generation of physical color objects with the help of dedicated software, which uses Standard Triangulate Language (STL) file format. The software is further used to slice the model into thin cross-sections to build part through layer by layer deposition (Haleem et al., 2016; Paul et al., 2018; Kim et al., 2018). This technology is used to produce physical three-dimensional models and has a wide range of applications in product design, development, education, medical research, etc. It is a generative technique, which uses the process of developing numerous products applicable in medical and biomedical engineering (Yongnian et al., 2009; Li et al., 2018). 3D printing technologies are the main components used in Industry 4.0. It expands its role toward sustainability, automation, manufacturing and in the medical field (Branger and Pang, 2015; Yang and Xu, 2018; Xu and Duan, 2019).
Color-jet 3D printing technology plays a significant role in new product development. It has the potential to reduce the cost and product development cycle time. This technology provides a valuable concept for rapid product development (Petrzelka and Frank, 2010; Javaid et al., 2015). By using AM technologies, products are manufactured according to the desired shape in lesser time and cost (Rylands et al., 2016; Nsengimana et al., 2019; Waterman and Dickens, 1994).
Experiments are being undertaken to use AM in the building and associated services to create specific features for building design. The building models are created to show colors, textures, and shapes. Additive manufacturing is used to produce components of the civil construction for concept development. These technologies are now available to print the part in five axes, which manufacture stronger parts (Shuaib et al., 2016; Haleem and Javaid, 2019c).
3D printing technologies can easily design and develop any product without the requirement of tooling/fixture. It can deal with printing of different materials at one time as per the specific requirements. As compared to the traditional manufacturing process, it can quickly change for the revised version of the product. It has greater flexibility for the manufacturing of any customized product/medical parts in lesser time and cost (Nsengimana et al., 2019; Ramola et al., 2019).
Researchers need to explore the applications of color-jet-printing 3D printing in the context of better-designed products and manufacturing complex parts as per the customer’s requirements. This technology manufactures part with the same product quality for different production volumes and can easily undertake to recycle raw material; as a result, there is lesser wastage of raw material. This technology eliminates various restrictions in design, which are previously faced by the manufacturers (Lia and Xu, 2003; Skawiński and Goetzendorf-Grabowski, 2019; Zhang et al., 2019).
2. Differentiating Subtractive Manufacturing from Additive Manufacturing
2.1. Subtractive manufacturing
Traditionally, through subtractive manufacturing, the construction of parts is done by successive removal of material manually or done through machining like CNC machines, where it uses multiple tools to cut-part in three axes, i.e. x-, y-, z-axis, such that one can reduce the total manufacturing time of the products with improved accuracy and repeatability (Singh and Singhal, 2016; Kataria et al., 2016). The main advantage of subtractive manufacturing is the ability to machine a wide variety of materials having different mechanical/physical properties with lower cost in a mass-production system. However, in this manufacturing process, material wastage is very high.
2.2. Additive manufacturing
In additive manufacturing, parts are printed by adding material layer by layer. In this process, we obtain the part data from the digital file (CAD), and in STL format, which is also used to build the part using contemporary technologies. AM has extensive use in product design and development, reverse engineering, inspection and allied processes (Bingham and Hague, 2013; Javaid and Haleem, 2019a); and is making an impact as a disruptive innovation (Cheng et al., 2018; Xu et al., 2018). In this process, material wastage is very low and supports customization. The significant benefits of AM technologies are as follows:
• | Customization: Additive manufacturing helps in product customization, providing higher levels of flexibility, thereby meeting specific demands of the individual customer (Deradjat and Minshall, 2015; Javaid and Haleem, 2019b). | ||||
• | Smaller lead time: AM technologies are used to save time in the manufacturing of the product with the help of rapid tooling processes. It has the potential to reduce lead time during customized manufacturing (Volpato and Childs, 2003; Kothman and Faber, 2016). | ||||
• | Material saving: These technologies help in overall material savings. It also undertakes efficient recycling of the raw material in different types of AM technologies, so the cost of the product gets reduced (Baechler et al., 2013; Grasso et al., 2018). | ||||
• | New material with better and customized properties: Additive manufacturing technologies fabricate part accurately by using new materials and their combinations to provide different properties (Lie et al., 2014; Liu et al., 2018). | ||||
• | Energy saving: Through AM technologies, there is a consumption of energy both in melting and then removing the excess material. In AM, consumption of electricity is dependent on the job duration. The construction time can be well optimized and thus lesser energy usage (Mognol et al., 2006). | ||||
• | Better built quality with improved accuracy: Dimensional accuracy is one of the essential requirements of product manufactured by any manufacturing process. Additive manufacturing can be used to provide better dimensional accuracy, and this remains the same for “n” numbers of parts. The dimensional accuracy and resolution of products made through AM are dependent on system parameters. Thus, with proper optimization and regulation, quality and accuracy of the final product improve (Turner and Gold, 2015; Paul et al., 2018). |
2.3. Major additive manufacturing technologies for part printing
The primary additive manufacturing technologies for 3D printing are as follows:
(i) | Stereolithography (SLA); | ||||
(ii) | Selective laser sintering (SLS); | ||||
(iii) | Fused deposition modeling (FDM); | ||||
(iv) | Direct metal laser sintering (DMLS); | ||||
(v) | Laminated object manufacturing (LOM); | ||||
(vi) | Multi-jet-printing (MJP) and poly jet 3D printing; | ||||
(vii) | Inkjet printing (IJP)/color-jet-printing (CJP). |
(i) | Stereolithography (SLA) In this process, the part is built with the help of material solidification through light-sensitive polymers exposed by UV radiation (Agarwal et al., 2006). The layer of the resin solidifies when a laser beam hits it. This process is iterative, and the final model printed by this technology needs post-processing. Surface finishing of the product is better and has lesser wastages of raw material (Gibson, 2017) and is used effectively for prototype development. | ||||
(ii) | Selective laser sintering (SLS) This technique uses a laser beam for melting and solidifying the part. The material used is in the form of powder, such as elastomers/metals (Borille et al., 2010). In this process, the laser beam is used to sinter the powdered material, layer by layer to build the desired shape of the product. | ||||
(iii) | Fused deposition modeling (FDM) In the FDM process, the object is manufactured by extruding specific types of polymers. In this process, two nozzles are used, where one is used to print the part, and another provides the support material (Borille et al., 2010). The material costs are lower when compared with other printing materials. The prototype can be made quickly by the addition of layers (Kumar et al., 2016b; Chohan et al., 2018). Nowadays, multi-nozzle FDM printing machines are available to print multi-materials at the same time at much higher temperature ranges (Chadha et al., 2019). | ||||
(iv) | Direct metal laser sintering (DMLS) DMLS is AM technology which builds a metal part. In this process, a laser beam is applied to sintered metal powder (material) to build a 3D solid object. A laser beam is directed to fuse the powder at defined points. This process produces metal parts with high accuracy, good surface quality, detail resolution, as well as mechanical properties (Rokicki et al., 2016). However, the cost of this technology is higher when compared with the other AM technologies. | ||||
(v) | Laminated object manufacturing (LOM) LOM technology generates a 3D part by adding layers of the defined sheet of materials (metal, plastic and paper). In this process, the CO2 laser is used to cut sheets of material as per the designed cross-section. After the removing of excess material from this sheet, another layer covers the previously manufactured layer, and the laser tracking will define the next pattern based on the information according to the STL file. The adhesive is used to combine the layers, and the 3D physical part is generated by repeating the steps (Kechagias, 2007). | ||||
(vi) | Multi-jet-printing (MJP) and poly-jet 3D printing (PJP) MJP and PJP technology employs photopolymer materials and UV bulbs. Each layer forms through a UV-curable acrylic plastic and in this process, the support material is also used. However, parts get separate during melting and washing process (Mancanares et al., 2015). | ||||
(vii) | Inkjet printing (IJP)/color-jet-printing (CJP) In color-jet-printing process, the part is manufactured by spreading material in the layer, over the build platform using a roller. The printing head jets a layer of binder on the material layer and iteratively the part develops after the solidification of the adhesives. The commercial version of CJP uses an automated iterative process for producing 3D parts/models, through spreading of powder on a base, and then selective bonding with the help of injecting an agglutinant (Mancanares et al., 2015; Gardan, 2017; Haleem and Javaid, 2019b). This technology has various advantages; like part production time is less and a variety of materials can be used as infilterent with lower product cost (Kumar et al., 2016a). It is helpful in bioprinting, especially in tissue printing. There are some limitations of this technology like low mechanical strength, and low surface quality of parts manufactured. This technology is also available for color 3D model, which is used for surgical planning in the medical field (Javaid and Haleem, 2017). |
3. Color-Jet 3D Printing: An Overview
Color-jet 3D printing is finding diversified applications including those in education, medical, design and prototype development before starting the full production. Technology is offered commercially in different models having different capabilities. All series in color-jet 3D printing share same control and hardware (Javaid et al., 2015). Advantages of CJP technology are listed as follows:
• | Ease of use; | ||||
• | Eco-friendly production processes; | ||||
• | Noiseless operation of the machine; | ||||
• | Variety of binders; | ||||
• | Variety of post-processing material and processes; | ||||
• | The process can be combined with high-performance composite materials; | ||||
• | Somewhat lower cost of part production. |
3.1. Working and steps followed in color-jet 3D printing
Color jet 3D printing machine deposits binders on successive layers of powder slices; this adhesive reacts with the powder (slice) and consolidates the 2D format of each printed section (Meira et al., 2013), these slices after adding consolidate a 3D model in the desired shape. Figure 1 shows the working principle of color-jet 3D printing.

Fig. 1. Working of color-jet 3D printing (adopted from Chandramohan and Marimuthu, 2011).
Several steps involved in producing parts through a color-jet technology are shown in the form of a block diagram (Fig. 2):

Fig. 2. Steps involved in color-jet 3D printing technology.
3.2. Alternative ways to print color products using additive manufacturing
There is an alternative technology for color 3D printing, where parts are built using multi-material photosensitive polymers. However, this technique is quite expensive. Colour FDM uses PLA filaments of different colours and software controls different nozzles. This paper does not consider FDM technology.
4. Objectives of the Paper
This article caters to the following research objectives:
(i) | Understanding the color-jet 3D technology in AM environment; | ||||
(ii) | Identifying the enablers, barriers and then the critical success factors (CSFs) in adopting color-jet printing for additive manufacturing; | ||||
(iii) | Providing the roadmap for the effective adoption of color-jet 3D printing technology. |
5. Control Variables in Color-Jet 3D Printing
In this paper, the focus is on color-jet 3D printing machine only. Thus, the factors so discussed are unique to this technology. However, some write-up is provided on the significant control variables of this type of 3D printing as subsection of this section.
5.1. Software
Software plays a significant role in product design and development. It helps to create/recreate designs as per the required dimensions. It helps to modify objects when scanned with the aid of the 3D scanner (Haleem and Javaid, 2018a). Machine software easily creates the product as per design changes in lesser time and help to improve product design quality. Different software such as CATIA, PRO-E, AUTODESK, Rhinoceros 3D, Solid Works, CREO, etc. are used for this designing process. The software is expensive and needs skilled persons for its efficient operating (Olatunji and Sher, 2015; Haleem et al., 2016).
5.2. Part orientation
Depending upon the part’s shape, an orientation helps to achieve better mechanical strength as well as reduce production time. The part is positioned horizontally or vertically on the build tray. For example, if a rod is printed, then slicing it in the x-axis, layer by layer, will provide better mechanical strength. Thus, with proper part orientation, one can reduce the time and overall cost of printing. Improper part orientation may create problems such as a decreased mechanical strength of the product and longer printing time (Farzadi et al., 2014; Haleem and Javaid, 2019a).
5.3. File slicing
Slicing is also a control variable of this technology. Product quality depends on the layer thickness and the quality of the printer head (Jamieson and Hacker, 1995; Boyard et al., 2018).
5.4. Material and its specification
Product quality is dependent upon the material (core) specification, which can be in the form of powder/liquid. Change of the material changes the product properties. Thus, improper material selection (specification) can be the primary barrier in color-jet 3D printing (Lie et al., 2014; Bass et al., 2016).
5.5. Machine maintenance
It requires extensive maintenance of machine parts, i.e. print head and lubrication of parts, greasing the piston screw and bearings to achieve smooth production. Before lubricating, make sure that all parts are clean. For maintenance, it needs a highly skilled person, which further increases the maintenance cost (Gerdes et al., 2016).
5.6. Support material
Support material plays a significant role in providing support to the product which has to be manufactured. In color-jet 3D printing, the support material is powder. Soluble (SCA-1200) is used as a support material in poly jet technology, which acquires the extra cost of the product (Wong and Hernandez, 2012; Boyard et al., 2018; Javaid and Haleem, 2019c).
5.7. The cost of printer
Cost of the 3D printing machine is the primary issue. Due to their high cost, small industries are not able to afford this machine. CJP has acquired less cost when compared with other AM technologies like DMLS (Bosque, 2015).
5.8. The cost of core material
Core material is used in the form of powder/liquid and requires protection while in storage. In this machine, material cost is high, which is only suitable for customized production system and not for the batch and continuous productions (Glasschroeder et al., 2015).
5.9. Limited material option
Machines offer a limited choice of raw material. Change in raw material creates chances to damage the machine (Lifton et al., 2014).
5.10. Limitation of the size of the finished product
There is a restriction on the size of the final product. The limitation is due to the size of the machine bed. However, machines are available with different bed sizes (Wei et al., 2016).
5.11. Lack of information
A significant number of customers do not have proper knowledge about 3D printing technologies and available machines. They do not understand its capability applications, input material and types of products that can be printed through them and the same is also true for the color-jet machine, and thus lack of proper information becomes a barrier (Bosque, 2015; Javaid and Haleem, 2019d).
5.12. Skilled manpower
Highly skilled workforce, who possesses sound knowledge of the software, selection of material, part processing, etc., is required to operate these machines (Bosque, 2015).
5.13. Binder
Liquid binder is dispensed through a print head and sprayed on the core material through jets of the print head. The variation of binder saturation value depends on the part geometry. One can modify the quality of binder to increasing strength of the part (Paula et al., 2013). Different types of binders used in color-jet 3D printing are:
• | Furan binder; | ||||
• | Phenolic binder; | ||||
• | Silicate binder; | ||||
• | Aqueous-based binder. |
5.14. Mechanical properties of product
The final product after printing is somewhat brittle and has low mechanical strength, thus requiring proper post-processing to provide necessary properties to the part. Post-processing makes this CJP technology somewhat different from other non-conventional machining processes (Katz et al., 2015).
5.15. Resolution and layer thickness
Resolution and layer thickness play a significant role, by decreasing layer thickness, the printed part loses mechanical strength (Farzadi et al., 2014). Post-processing is used to tackle this problem.
5.16. The speed of printing of customized product
This technology has faster speed and is suitable for producing customer order production (Steenhuis and Pretorius, 2016).
5.17. The cost of product manufacturing
Printing is beneficial for customized products when compared with other traditional mass manufacturing systems (Steenhuis and Pretorius, 2016). It prints the new concepts and design colorfully, making the prototype development cheaper, simpler and effective (Javaid et al., 2019).
5.18. Post-processing and infiltrate
This step is necessary for removing the support material and enhancing the surface finish and strength of the part. The product manufactured by this technology requires post-processing/finishing process to obtain the required properties. The final printed model is dried and cleaned; then dipped in the post-processing liquid material to impart required properties/strength. This post-processing increases the product cost but is advantageous. There are different types of post-processing liquids/binders available to give requisite properties and surface finish to the product so produced (Agarwala et al., 1995; Lie et al., 2014). Various types of infiltrate used in CJP machines are as follows:
• | Epoxy; | ||||
• | Medical grade silicone; | ||||
• | Electroplating; | ||||
• | Epsom salt; | ||||
• | Room temperature vulcanization (RTV) molding; | ||||
• | Metalizing. |
Post-processing is also broadly classified as post-processing using water cure and post-processing with color bond
• | Post-processing using water cure: Water curing is one of the best ways to finish the concept model. Water curing is done with Epsom salt, here no restricted or hazardous chemicals are involved. Epsom salt gets dissolved into tap water, and the fine mist is sprayed to the part to achieve a limited hardness, smoothen its surface and make a good appearance of the product (Begines et al., 2016). | ||||
• | Post-processing with color bond: Post-processing of the parts using color bond is one of the unique selling points of this technology. This color post-processing is done with the help of the dipping method, whereby it imparts color along with mechanical properties to the part. However, post-processing increases product cost (Agarwala et al., 1995). |
6. CSFs for Practical Usage of Color-Jet 3D Printing
Product design cycle time is critical for faster and accurate conceptualizing of the part in physical shape. It helps in reverse engineering, concept-elaboration, understanding the design change, feeling the design and assisting in customizing/conceptualizing the models. The machine is not only for producing the same items but also for providing new manufacturing applications. Table 1 elaborates the CSFs of color-jet 3D printing along with their contribution to the additive manufacturing area.
S. no. | Critical success factors | Reference | Contribution to color-jet 3D printing | ||||||||||||||||||
---|---|---|---|---|---|---|---|---|---|---|---|---|---|---|---|---|---|---|---|---|---|
1 | Software | Olatunji and Sher (2015); Boyard et al. (2018); Haleem and Javaid (2018b) |
| ||||||||||||||||||
2 | Part orientation | Farzadi et al. (2014) |
| ||||||||||||||||||
3 | Binder | Paula et al. (2013) |
| ||||||||||||||||||
4 | Post-processing material (surface coating) | Agarwala et al. (1995) |
| ||||||||||||||||||
5 | Machine maintenance | Gerdes et al. (2016) |
| ||||||||||||||||||
6 | Core material | Glasschroeder et al. (2015) |
| ||||||||||||||||||
7 | File slicing | Jamieson and Hacker (1995) |
| ||||||||||||||||||
8 | Cost of part production | Steenhuis and Pretorius (2016) |
| ||||||||||||||||||
9 | Hardware | Conner et al. (2015) |
| ||||||||||||||||||
10 | Cost of machine and tooling | Kumar et al. (2016a; 2016b) |
| ||||||||||||||||||
11 | Accuracy and quality of the final product | Castilho et al. (2015) |
| ||||||||||||||||||
12 | Color and texture of the printed part | Stanic et al. (2012) |
|
CSFs for the effective adoption of color-jet 3D printing have been identified methodically, using literature review assisted by experts. The initial screening has been done through the analysis of enablers and barriers of color-jet 3D printing (refer to Table 2). The structural and hierarchical model is further developed using the contextual relationship among the CSFs.
S. no. | CSFs | Function | Enabler | Barrier | References | ||||||||||||||||||||||||||||||||||||||||||||||||
---|---|---|---|---|---|---|---|---|---|---|---|---|---|---|---|---|---|---|---|---|---|---|---|---|---|---|---|---|---|---|---|---|---|---|---|---|---|---|---|---|---|---|---|---|---|---|---|---|---|---|---|---|---|
1 | Software |
|
|
| Lifton et al. (2014); Aroca et al. (2017); Muir and Haddud (2018) | ||||||||||||||||||||||||||||||||||||||||||||||||
2 | Part orientation |
|
|
| Yang et al. (2017); Zhang et al. (2016) | ||||||||||||||||||||||||||||||||||||||||||||||||
3 | Binder |
|
|
| Chen and Zhao (2016); Steenhuis and Pretorius (2016) | ||||||||||||||||||||||||||||||||||||||||||||||||
4a | Post-processing |
|
|
| Impens and Urbanic (2016) | ||||||||||||||||||||||||||||||||||||||||||||||||
4b | Post-processing using water cure |
|
|
| Begines et al. (2016) | ||||||||||||||||||||||||||||||||||||||||||||||||
4c | Post-processing with color bond |
|
|
| Hancock and Lin (2004); Banga et al. (2018) | ||||||||||||||||||||||||||||||||||||||||||||||||
5 | Machine maintenance |
|
|
| Gerdes et al. (2016) | ||||||||||||||||||||||||||||||||||||||||||||||||
6 | Material core and specification |
|
|
| Glasschroeder et al. (2015) | ||||||||||||||||||||||||||||||||||||||||||||||||
7 | File slicing |
|
|
| Zhang and Joshi (2017); Hayasi and Asiabanpour (2014) | ||||||||||||||||||||||||||||||||||||||||||||||||
8 | Cost of part production |
|
|
| Baldinger et al. (2016) | ||||||||||||||||||||||||||||||||||||||||||||||||
9 | Hardware speed |
|
|
| Brajlih et al. (2011) | ||||||||||||||||||||||||||||||||||||||||||||||||
10 | Cost of machine |
|
|
| Weiss et al. (2015) | ||||||||||||||||||||||||||||||||||||||||||||||||
11 | Accuracy and quality of the final product |
|
|
| Stopp et al. (2008); Haleem et al. (2016) | ||||||||||||||||||||||||||||||||||||||||||||||||
12 | Color and texture of the part produced |
|
|
| Yuan et al. (2017) |
7. Structural and Hierarchical Model of “Part Manufacturing Through Color-Jet 3D Printing”
Analysis of CSFs is essential, as it provides the understanding of its practical applicability and adaptability of 3D CJP technology. Through the critical review of literature and discussion with the experts, we identified principal actors like enablers, barriers, and CSF of this technology. These CSFs are inter-related and hierarchical. Thus, ISM seems to be an appropriate tool for structured modeling Khan et al. (2014).
7.1. Model making through interpretative structural modeling (ISM) technique
An ISM deals with the interpretation of the embedded representation system by systematic, iterative application of graph theory resulting in a directed graph for the complex system for a given contextual relationship among a set of elements. ISM can be defined as a process that transforms unclear and poorly articulated mental models of systems into visible, well-defined models useful for many purposes. In any interpretive structural model, the interpretation of the digraph is made at two levels, i.e. at nodes and links (Lal and Haleem, 2009; Sushil, 2012; Jharkharia and Ravi, 2007).
If there is a directed relationship in an ISM from objective A to objective B, thereby implying that objective A will help achieve objective B, it does not interpret that in what way objective A will help achieve objective B.
ISM has become a computer-assisted interactive learning process whereby structural models are produced and studied (Haleem and Khan, 2017; Xu, 2000a). Structural models so produced portray the structure of a complicated issue, a system, or a field of study in carefully designed patterns employing graphics and words. ISM is primarily intended as a group learning process and is based on the relational mathematics, which clarifies and transforms ill-structured mental models of the system under study into a clear interrelated structured set of system elements (Ravi and Shankar, 2005).
Any suitable group learning/judgment process can be used for developing the contextual relationships, e.g. brainstorming, nominal group technique (NGT), etc. Here, a contextually relevant subordinate relation is chosen. It should be subordinate in the sense that a direction should be attached to it and phrased as to lead to paired comparisons (Xu, 2000b; Luthra et al., 2011). Group judgment on the paired comparison is determined through the consensus of the majority during the discussion and considering the transitivity among the elements after getting the inputs in making the model.
ISM is a system-based methodology, which represents the group’s view. This article analyzes the views compiled, through an “idea engineering workshop” and the available literature. Table 3 depicts the expert’s opinion on the role of different CSFs on the effective adoption of 3D printing technology. Here, four symbols are used to denote the direction of the relationship between enabler (i and j)
S. no. | Critical success factors | 12 | 11 | 10 | 9 | 8 | 7 | 6 | 5 | 4 | 3 | 2 | 1 |
---|---|---|---|---|---|---|---|---|---|---|---|---|---|
1 | Software | O | O | X | V | O | V | V | V | V | V | V | |
2 | Part orientation | V | V | A | A | V | X | A | A | X | X | ||
3 | Binder | V | V | O | A | V | X | A | A | X | |||
4 | Post-processing material | V | V | A | A | V | X | A | A | ||||
5 | Machine maintenance | V | V | A | X | V | V | X | |||||
6 | Core material | V | V | A | X | V | V | ||||||
7 | File slicing | V | V | A | A | V | |||||||
8 | Cost of part production | X | X | O | A | ||||||||
9 | Hardware | V | V | A | |||||||||
10 | Cost of machine | V | V | ||||||||||
11 | Accuracy and quality of the final product | X | |||||||||||
12 | Color and texture of the part produced |
V: CSF i will help in achieving CSF j and vice versa is not true. | |||||
A: CSF j will be significant in achieving CSF i and vice versa is not true. | |||||
X: CSF i and CSF j will help in achieving each other. | |||||
O: CSF i and CSF j are not related. |
Table 4 gives the values of the initial reachability matrix, and the same is derived from structural self-interaction matrix. Further, the final reachability matrix is shown in Table 5, which also takes care of the transitivity among the elements.
Critical success factors | 1 | 2 | 3 | 4 | 5 | 6 | 7 | 8 | 9 | 10 | 11 | 12 |
---|---|---|---|---|---|---|---|---|---|---|---|---|
1 | 1 | 1 | 1 | 1 | 1 | 1 | 1 | 0 | 1 | 1 | 0 | 0 |
2 | 0 | 1 | 1 | 1 | 0 | 0 | 1 | 1 | 0 | 0 | 1 | 1 |
3 | 0 | 1 | 1 | 1 | 0 | 0 | 1 | 1 | 0 | 0 | 1 | 1 |
4 | 0 | 1 | 1 | 1 | 0 | 0 | 1 | 1 | 0 | 0 | 1 | 1 |
5 | 0 | 1 | 1 | 1 | 1 | 1 | 1 | 1 | 1 | 0 | 1 | 1 |
6 | 0 | 1 | 1 | 1 | 1 | 1 | 1 | 1 | 1 | 0 | 1 | 1 |
7 | 0 | 1 | 1 | 1 | 0 | 0 | 1 | 1 | 0 | 0 | 1 | 1 |
8 | 0 | 0 | 0 | 0 | 0 | 0 | 0 | 1 | 0 | 0 | 1 | 1 |
9 | 0 | 1 | 1 | 1 | 1 | 1 | 1 | 1 | 1 | 0 | 1 | 1 |
10 | 1 | 1 | 0 | 1 | 1 | 1 | 1 | 0 | 1 | 1 | 1 | 1 |
11 | 0 | 0 | 0 | 0 | 0 | 0 | 0 | 1 | 0 | 0 | 1 | 1 |
12 | 0 | 0 | 0 | 0 | 0 | 0 | 0 | 1 | 0 | 0 | 1 | 1 |
Critical success factors | 1 | 2 | 3 | 4 | 5 | 6 | 7 | 8 | 9 | 10 | 11 | 12 | Driving power |
---|---|---|---|---|---|---|---|---|---|---|---|---|---|
1 | 1 | 1 | 1 | 1 | 1 | 1 | 1 | 1a | 1 | 1 | 1a | 1a | 12 |
2 | 0 | 1 | 1 | 1 | 0 | 0 | 1 | 1 | 0 | 0 | 1 | 1 | 7 |
3 | 0 | 1 | 1 | 1 | 0 | 0 | 1 | 1 | 0 | 0 | 1 | 1 | 7 |
4 | 0 | 1 | 1 | 1 | 0 | 0 | 1 | 1 | 0 | 0 | 1 | 1 | 7 |
5 | 0 | 1 | 1 | 1 | 1 | 1 | 1 | 1 | 1 | 0 | 1 | 1 | 10 |
6 | 0 | 1 | 1 | 1 | 1 | 1 | 1 | 1 | 1 | 0 | 1 | 1 | 10 |
7 | 0 | 1 | 1 | 1 | 0 | 0 | 1 | 1 | 0 | 0 | 1 | 1 | 7 |
8 | 0 | 0 | 0 | 0 | 0 | 0 | 0 | 1 | 0 | 0 | 1 | 1 | 3 |
9 | 0 | 1 | 1 | 1 | 1 | 1 | 1 | 1 | 1 | 0 | 1 | 1 | 10 |
10 | 1 | 1 | 1a | 1 | 1 | 1 | 1 | 1a | 1 | 1 | 1 | 1 | 12 |
11 | 0 | 0 | 0 | 0 | 0 | 0 | 0 | 1 | 0 | 0 | 1 | 1 | 3 |
12 | 0 | 0 | 0 | 0 | 0 | 0 | 0 | 1 | 0 | 0 | 1 | 1 | 3 |
Dependence power | 2 | 9 | 9 | 9 | 5 | 5 | 9 | 12 | 5 | 2 | 12 | 12 | 91 |
1a= Transitivity. |
Level partitioning is undertaken and shown in Tables 6–9. Thus, the structural model is shown in Fig. 3.
Critical success factors | Reachability set | Antecedent set | Intersection | Level |
---|---|---|---|---|
1 | 1,2,3,4,5,6,7,8,9,10,11,12 | 1,10 | ||
2 | 2,3,4,7,8,11,12 | 1,2,3,4,5,6,7,9,10 | ||
3 | 2,3,4,7,8,11,12 | 1,2,3,4,5,6,7,9,10 | ||
4 | 2,3,4,7,8,11,12 | 1,2,3,4,5,6,7,9,10 | ||
5 | 2,3,4,5,6,7,8,9,11,12 | 1,5,6,9,10 | ||
6 | 2,3,4,5,6,7,8,9,11,12 | 1,5,6,9,10 | ||
7 | 2,3,4,7,8,11,12 | 1,2,3,4,5,6,7,9,10 | ||
8 | 8,11,12 | 1,2,3,4,5,6,7,8,9,10,11,12 | 8,11,12 | I |
9 | 2,3,4,5,6,7,8,9,11,12 | 1,5,6,9,10 | ||
10 | 1,2,3,4,5,6,7,8,9,10,11,12 | 1,10 | ||
11 | 8,11,12 | 1,2,3,4,5,6,7,8,9,10,11,12 | 8,11,12 | I |
12 | 8,11,12 | 1,2,3,4,5,6,7,8,9,10,11,12 | 8,11,12 | I |
Critical success factors | Reachability set | Antecedent set | Intersection | Level |
---|---|---|---|---|
1 | 1,2,3,4,5,6,7,9,10 | 1,10 | ||
2 | 2,3,4,7 | 1,2,3,4,5,6,7,9,10 | 2,3,4,7 | II |
3 | 2,3,4,7 | 1,2,3,4,5,6,7,9,10 | 2,3,4,7 | II |
4 | 2,3,4,7 | 1,2,3,4,5,6,7,9,10 | 2,3,4,7 | II |
5 | 2,3,4,5,6,7,9 | 1,5,6,9,10 | ||
6 | 2,3,4,5,6,7,9 | 1,5,6,9,10 | ||
7 | 2,3,4,7 | 1,2,3,4,5,6,7,9,10 | 2,3,4,7 | II |
9 | 2,3,4,5,6,7,9 | 1,5,6,9,10 | ||
10 | 1,2,3,4,5,6,7,9,10 | 1,10 |
Critical success factors | Reachability set | Antecedent set | Intersection | Level |
---|---|---|---|---|
1 | 1,5,6,9,10 | 1,10 | ||
5 | 5,6,9 | 1,5,6,9,10 | 5,6,9 | III |
6 | 5,6,9 | 1,5,6,9,10 | 5,6,9 | III |
9 | 5,6,9 | 1,5,6,9,10 | 5,6,9 | III |
10 | 1,5,6,9,10 | 1,10 |
Critical success factors | Reachability set | Antecedent set | Intersection | Level |
---|---|---|---|---|
1 | 1,10 | 1,10 | 1,10 | IV |
10 | 1,10 | 1,10 | 1,10 | IV |

Fig. 3. Structural hierarchical model of CSFs for the adoption of CJP printing technology.
From the level partitioning, a digraph is developed; then transitivity links are eliminated, and nodes are replaced by corresponding CSF numbers to build the final structural model of CSF in adopting the color-jet technology.
8. MICMAC Analysis
Matrices impacts cruises-multiplication appliqué’ and classmate (cross-impact matrix multiplication applied to classification) is abbreviated as MICMAC. This analysis depicts the degree of dependence power on one axis and driving power on another axis (kindly refer to Fig. 4). Here the sum of “1s” in the row (taken from final reachability matrix) for all the corresponding variables gives the driving power. Similarly, the sum of “1s” in the columns provides dependence power. For further analysis of the ISM, driving and dependence graphs are drawn, and the same is shown in Fig. 4. This graph shows four clusters of CSF through four of its quadrants.
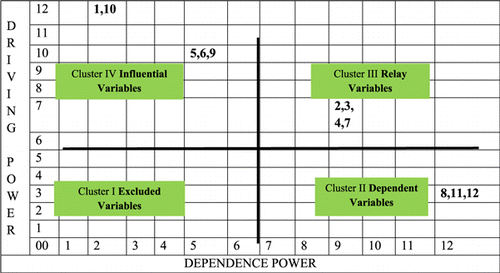
Fig. 4. Driving and dependence graph of CSFs.
8.1. Excluded variables
The first cluster, which lies in the lower left quadrant, has autonomous barriers which show weak driver potential and weak dependence power. In this study, no barrier falls in this cluster.
8.2. Dependent variables
The second cluster, which lies in the lower right quadrant, has dependent barriers having weak driver potential, but high dependence. Cost of part production, accuracy and quality of final product, and color and texture of the part produced fall in this category.
8.3. Relay variables
The third cluster, which lies on upper right quadrant, consists of linkage barriers having reliable driver power and high dependence also. Post-processing material, part orientation, binder, and file slicing fall in this category.
8.4. Influential variables/important variables
The fourth cluster lies in the upper left quadrant and depicts independent driving barriers that have strong driving power but weak dependence. Software, cost of machine, machine maintenance, core material, hardware fall under this category.
9. Results, Discussion, and Scope for Future Work
Color-jet 3D printing technology seems suitable for implementing digital manufacturing systems. It imparts flexibility in designing, manufacturing, and undertaking associated activities. The significant findings are as follows:
(i) | In traditional mass production, product customization is low, and the cost of the product is also comparatively low, but the cost of prototype development is quite high. However, this technology provides prototypes at a lower cost; here, the unit cost of production remains the same for “n” number of items. | ||||
(ii) | This technology seems appropriate for producing innovative prototypes and customized products, especially product design and development or prototype development. | ||||
(iii) | It manufactures products that look (natural) colorful, accurate, smooth parts, prototypes, and tooling and can be used for digitally optimized manufacturing. | ||||
(iv) | This technology seems to have a proper scope in medical, product design, and analysis. | ||||
(v) | To improve the application, one has to identify a better post-processing material, binder, and also the core. The contemporary binders are organic compounds and different types of furans, phenolic binders, silicate, aqueous, etc. | ||||
(vi) | The post-processing is undertaken through the epoxy, resin, medical-grade, silicon, Epsom salt, RTV molding, metallizing, and electroplating. | ||||
(vii) | The file slicing helps to improve various parameters of cost and quality, it is controlled by dedicated software and hardware, and this requires sophisticated controlled systems. | ||||
(viii) | The most prominent driver is the cost of the machine, tooling, and software and is evident from Table 10, showing the difference in driving power and dependence power of CSFs. | ||||
(ix) | With higher demand and ongoing research and development in making this technology, the machine and product cost will come down. | ||||
(x) | Software and the machine cost are the primary drivers for this color-jet printing technology that helps in providing the product at a lower price. | ||||
(xi) | There is a need for developing better core material, software, and the associated machine hardware. | ||||
(xii) | The main advantages of this technology are accuracy and color texture of the part produced. Post-processing material can assist in a big way toward providing different properties to the part. |
S. no. | Critical success factor | Driving power | Dependence power | Effectiveness = (Driving power − Dependence power) |
---|---|---|---|---|
1 | Software | 12 | 2 | 10 |
2 | Part orientation | 7 | 9 | −2 |
3 | Binder | 7 | 9 | −2 |
4 | Post-processing material | 7 | 9 | −2 |
5 | Machine maintenance | 10 | 5 | 5 |
6 | Core material | 10 | 5 | 5 |
7 | File slicing | 7 | 9 | −2 |
8 | Cost of part production | 3 | 12 | −9 |
9 | Hardware | 10 | 5 | 5 |
10 | Cost of machine and tooling | 12 | 2 | 10 |
11 | Accuracy and quality of the final product | 3 | 12 | −9 |
12 | Color and texture of the part produced | 3 | 12 | −9 |
If part orientation, binder, file-slicing, and post-processing are appropriately researched and managed, then one can obtain improved accuracy, texture and reduced cost of the part. It is observed that none of the CSF is in the autonomous region. Thus, machine maintenance, machine hardware, and the core material become influential when combined with software.
Color-jet 3D printing technology seems somewhat expensive, and for better customer acceptance, it should be developed as cost-competitive. Presently, the infiltrate and post-processing materials are limited and getting metal-like properties in the product is difficult. The gypsum powder has its own limitations of mechanical properties, which are to be augmented through post-processing. Thus, there is a need for extensive multidisciplinary research in this area, and even there is requirement of changing the core material.
A wide variety of products can be developed using color-jet 3D printing technology. Here, one can develop ergonomically suited tooling, tools for medical applications, implants, realistic prototypes, etc.
Various products require modification for improved performance than that of the existing, such as industrial products, medical products, instruments and this can well be obtained with the help of this technology (Steenhuis and Pretorius, 2017). By using this, there is a reduction in the product development cycle time and improvement in the design and quality of the final product. The same can be implemented efficiently with AM when compared with the traditional machining process. Thus, companies tend to be able to deliver new products at a cheaper and faster rate and create the design with less investment and lesser tooling. This technology has a scope in the medical applications, product design and analysis, prototype development, and reverse engineering.
10. Conclusion
Through this paper, CSFs for the effective adoption of CJP 3D printing technology are identified using an extensive literature review complemented with expert opinion. Further, a hierarchal structural model of the CSFs to the adoption of CJP is developed using ISM. A brief write-up about these CSFs is provided for a better understanding of this technology. By deploying this technology, one can obtain an interesting part with somewhat better accuracy in lesser time. ISM has been selected as a structural modeling tool because few domain experts are available. This model is analyzed by MICMAC, which gave us a better understanding of the roadmap of implementing CJP for a higher level of customer acceptance. This technology has extensive use in product design and development and especially in prototype development. However, the part produced needs post-processing, this lowers down the mechanical strength. Therefore, the primary barrier to adoption of this technology by industry is mechanical strength. Further, it is felt for a need for extensive research and development on various aspects as identified through the model and its analysis. Digital optimization of design (DoD) is the ultimate goal of AM, which can be achieved through appropriate usage of color-jet 3D printing technology.