Industry 4.0: The Case-Study of a Global Supply Chain Company
Abstract
The technological evolution that enterprises are facing is increasingly fast and dynamic, demanding more and more flexibility and agility in the application of new technologies in an increasingly globalized and competitive business environment. This work has a broad view of the industry 4.0 influence in the global supply chain companies, as it is essential for long-term business sustainability and one of the key drivers of profitability and growth. The model proposed in this research effort considers the application in the processes of a global supply chain enterprise, which includes from the beginning of the demand request, also the industrial activities, to the post-sale analysis; finally, an unprecedented indicator was developed to measure the level of application of industry 4.0 concepts in organizations according to the state-of-the-art in the evaluated processes. Then, the model was applied to the real case of a global high-tech supply chain company. The first findings demonstrate the ease of understanding and applicability of the model for companies to analyze the digital transformation in their processes and identify gaps to convert them into real opportunities to leverage their business.
1. Introduction
In an increasingly competitive scenario with a dynamic and globalized economy, manufacturing companies around the world are facing substantial challenges due to recent environmental, social, economic and technological developments where market conditions tend to change, whether due to new consumer needs, new competitors, changes in the market or economic policies, manufacturing enterprises need to not only become, but also remain competitive to ensure their survival.
Industry 4.0 has revolutionized the traditional production line toward smart factories in a sustainable environment. It represents an intelligent manufacturing network, where machines and products interact without human control. Industry 4.0 technologies enable the seamless information transfer between multiple stakeholders in the supply network (Gorkhali, 2022).
The data generated in many stages of supply chain enterprises from design (or demand start) to after-sales was collected, analyzed and used to support business decisions in many sectors, customer behavior and inventory (Davenport and Dyché, 2013) creating one of the most valuable assets (Knowledge Management) that can define a company’s competitiveness since the modern industry beginning, perhaps even earlier (Côrte-Real et al., 2017).
Exploiting the full potential of this scenario is supported by technological advances in data collection, new organization forms which are creating the new environment with large data volumes for leading companies to build capacity in new areas knowledge to become more intelligent companies (Malladi, 2013).
In view of recent technological developments and an increasing demand scenario for personalized products, greater complexity, higher quality and reduced costs; the emergence of a new industry model has become essential to maintain the companies’ competitiveness (Hermann et al., 2016).
The current state-of-the-art in production technology can be described as driven mainly by increased efficiency over manufacturing processes. However, this focus on advances in manufacturing efficiency occurs in the individual company instead of the entire supply chain (Schumacher et al., 2016).
Advances can also be seen at the organizational-economic level as Lean Management at the manufacturing technology level, i.e., Laser technology, additive manufacturing, robotics integrates with virtual reality (De Weck et al., 2014) in material level, information technology level, i.e., RFID, embedded systems. All these advances have led to significant gains, but isolated in the process, efficiency and product quality.
Garay-Rondero et al. (2020) synthesized the main actors that impact supply chain companies being (i) Management Components such as Planning and Control Methods, communication and information (ii) flows such as materials, information, finance (iii) Network structures such as logistics, distribution and (iv) Management process such as managing suppliers, customers, demand which associated with the main industry 4.0 components accelerate a future vision connectivity between different supply chain digitization in order to add value through new cooperation forms and digital integration.
The production processes integration must take place at the horizontal level (across the entire value chain) and at the vertical level (in all automation layers). Fully integrated and factories, machines, processes and networked products will then be able to act intelligently and partially autonomously that requires minimal manual interventions (Monostori, 2014).
Recent concepts like internet of things, cloud-based manufacturing (Gao et al., 2015) and smart factories meet these requirements in part and are commonly used under the visionary industrial revolution concepts (Berger, 2014).
Industry 4.0 refers to recent technological advances where the internet and supporting technologies (i.e., embedded systems) serve to integrate physical objects, human actors, intelligent machines, production lines and processes across organizational boundaries to form a new kind of intelligence, networked and agile supply chain value.
Experiences from several strategic orientation workshops showed that enterprises have serious problems in understanding the general industry 4.0 idea and apply the concepts in the real business life (Erol et al., 2016), on the other hand, there is evidence that when consistently implemented Industry 4.0 has a positive impact in operational performance, including cost performance, quality, delivery and flexibility (Szász et al., 2020).
Enterprises face problems in determining their state of development in relation to the industry 4.0 vision and, therefore, fail to identify specific action fields, programs and projects. Overcome growing uncertainty and dissatisfaction in manufacturing companies in relation to the industry 4.0 idea, new methods and tools are needed to provide guidance and support for aligning business strategies and operations (Schumacher et al., 2016).
So, we have the research question that most affects companies in the global supply chain: How are global supply chain enterprises getting ready to take advantage of the industry 4.0 environment to generate real value? Our spectrum of view is not concentrated only in assessing industrial activities, but in all operations that involve a global company, therefore, from the beginning of the demand request to the post-sale analysis; based on this question this work purpose is developed.
The objective of this research effort is to analyze a traditional company in the global supply chain manufacturing industry and provide a maturity model with a broad processes analysis, not restricting industrial activities, and through an assessment to identify gaps and provide information that allows discussion to take advantage of the potential of Industry 4.0 in your processes.
This study will be valuable to support the transformation industry’s path in the new technological era, providing the experience and best practices in the preparation of the enterprise and enhancing the knowledge that is important to reduce the response time to the most diverse demands, increase its efficiency and improve your competitiveness.
The paper is structured as follows. Initially, we discuss the concepts that culminate in industry 4.0 as well as demonstrating the evolution in the academic environment. Then, we describe the macro-processes, and respective details, which involve the company considered as well as conceptual bases of the structure of the proposed model. The results presented in the model and in the first findings of the preliminary assessment carried out in the case study are presented. Finally, we conclude with a discussion of the main findings and the linear knowledge continuity is proposed as future research.
2. Literature Review
2.1. The industrial revolutions
The Industry 4.0 concept originates from a strategic project by the German government with a focus on technology. The term was first used at the Hannover Fair in 2011 (Drath and Horch, 2014). Later, final report on recommendations for implementing Industry 4.0 was published by the German government to capture opportunities and maintain leadership in the manufacturing engineering industry (Xu et al., 2018).
The term industry 4.0 refers to the fourth industrial revolution when evaluating the most abrupt changes that we had in the sector during the humanity evolution, while the first industrial revolution (1780) was driven mechanical looms design powered by steam engines and resulted in the production centralization process in factories.
After 100 years of steam engines, the second revolution took place, being identified by production lines insertion for the construction of the automotive model Ford T; the third industrial revolution took place in the late 1960s, identified by the presentation of the first programmable logic controller, which allows the programming of digital systems (Pereira and de Oliveira Simonetto, 2018).
Following the evolutionary cycle, the fourth industrial revolution, represented by industry 4.0, has the basic foundation connecting machines, systems and assets having as objectives: to improve products and/or services; reduce costs; manage operations more efficiently thanks to production performance monitoring; to better position yourself in the competition for accessing data and information useful for fasting and better response to market needs (Moeuf et al., 2018).
In this way, applied to companies, they will be able to create smart grids throughout the supply chain that can control production modules autonomously. In other words, smart factories will have the capacity and autonomy to schedule maintenance, predict process failures and adapt to requirements and unplanned changes in production systems.
2.2. Industry 4.0 principles and pillars
Industry 4.0 has been changing technological reality in manufacturing. The smart industry arises as a new digital systems pattern, information technology and internet solutions (Oliveira et al., 2020).
The industry 4.0 field study is relatively new (close to ten years), we can say that in the second half of this time there were greater studies contributions, thus evaluating the documents most cited in the literature in the last 5 years (2016–2020).
From these studies, we can highlight the main concepts provided, which are: ability to operate in real time: it consists of the acquisition and data treatment almost instantly, allowing decision making in real time; virtualization: simulations used and also supervisory systems.
Thus, industry 4.0 proposes the smart factories existence that allow tracking and remote monitoring of all processes through the various sensors spread across the industrial plants (i.e., factories, warehouse) and decentralization, in this way decision-making can be made through systems according to production needs and in real time. Furthermore, machines and industrial processes do not receive commands, but are able to provide information about their work cycle and improve their performance through machine learning (Rüßmann et al., 2015).
In this way, the smart factory modules work decentrally to improve production processes, another relevant concept is flexibility: production according to demand, coupling and decoupling of production modules, i.e., quickly change-over (Moeuf et al., 2018).
What offers flexibility to easily change machine tasks is system integration which in turn is characterized by three dimensions: (i) vertical integration—takes place within the smart factories, where the people connection, objects and systems in the “smart” factories leads dynamic value networks creation; (ii) horizontal integration—occurs through value networks, starts to use new technologies to exchange and manage information between stakeholders in the process, allowing for closer collaboration between customers, suppliers and business partners and (iii) digital integration—end to end is made possible by vertical and horizontal integrations, which take place from the information collection about the product throughout its life cycle and add value from conception to outbound logistics (Rüßmann et al., 2015).
Based on the above principles, industry 4.0 is a reality made possible by technological advances in the last decade, combined with technologies in development in the areas of information technology knowledge and engineering (Xu et al., 2018).
The technological pillars that support Industry 4.0 can be summarized as follows (Lasi et al., 2014): (i) Internet of things (IoT): Consists in the network connection of physical objects, environments, vehicles and machines by means of embedded electronic devices that allow data collection and exchange, (ii) Cyber-physical Systems (CPS): These are systems that work based on the Internet of Things and are equipped with sensors and actuators and (iii) Big Data analytics: They are very extensive and complex data structures that use new approaches for the capture, analysis and information management.
Applied to industry 4.0, Big Data technology consists of 6Cs to deal with relevant information: Connection (to the industrial network, sensors and PLCs), Cloud (cloud/data on demand), Cyber (model and memory), Content, Community (information sharing) and Customization (personalization and values) and (iv) Security: One of the key challenges for the success of the fourth industrial revolution is the security and information systems robustness. Problems such as transmission failures in machine–machine communication, or even eventual system failures that can cause production problems. With all the connectivity established, systems will also be needed to protect the company’s know-how, contained in the process control files (Kagermann et al., 2013).
Finally, industry 4.0 is changing the technological enterprises reality. The smart industry emerges as a new standard for digital systems, information technology and internet solutions. The industry 4.0 impacts are multifaceted and complex for all organizations and economies. In addition to the changes, industry 4.0 brings a new organizational dynamic: fewer operational processes implying new job skills and more efficient results (Rafael et al., 2020).
2.3. Industry 4.0 applied in many fields
The 4.0 industry concepts have been a growing issue in academic publications, Fig. 1 shows the publications evolution since 2011, when we had the first formal document at the Hannover fair, and until end of 2020, when we used the terms “industry 4.0” or “advanced manufacturing”, the most common terms used, the Scopus database was used, the publications growth went from 1,174 documents (2011) to 8,351 (2020).
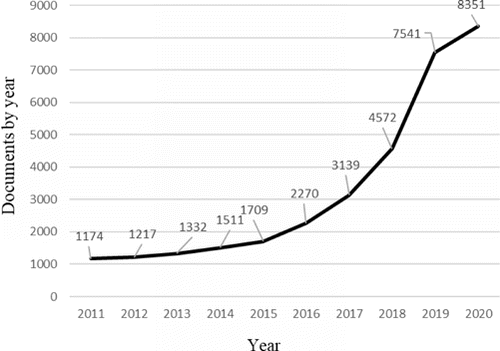
Fig. 1. Number of publications using “industry 4.0” or “advanced manufacturing”.
The industry 4.0 concepts have been the studies subject in several areas and applications in the most economy sector, i.e., technological assistance to workers to maximize the benefit of the varieties that this type of technology has (Gorecky et al., 2014), blockchain application to facilitate machine-to-machine interaction in the chemical industry (Sikorski et al., 2017) for creating smart products (Schmidt et al., 2015), associated with lean manufacturing (Sanders et al., 2016), application for healthcare (Pace et al., 2018), in agriculture sector (Zambon et al., 2019), automotive industry (Lin et al., 2018), aerospace (Ceruti et al., 2019) and in higher education (Li, 2020); thus, in addition to the increase in publications involving industry 4.0, there is also greater dissemination in several knowledge areas.
Some maturity models were found that seek to evaluate industry 4.0 in organizations, however, through bibliometrics that uses citation level evaluation in the research bases in the last five years (2016–2020), as can be seen in Table 1, they were directed to enable the industry 4.0 evaluation or the strategy or even in the evaluation of some specific processes, many studies analyzed do not describe the methodology used in this way were not considered.
Author(s) | Main findings | Author(s) | Main findings |
---|---|---|---|
Schumacher et al. (2016), Schumacher et al. (2019) | Evaluates the company’s strategy and the level of use of enabling technologies, there is no discrimination by company processes. | Canetta et al. (2018) | The model is available to evaluate the use of enabling technologies of industry 4.0 in companies. |
Lanza et al. (2016) | Evaluation as a quick check and part of a process model for performing gap analysis to overcome barriers through a toolbox; no details about items and development process offered. | Asdecker and Felch (2018) | Model that specifically analyzes the processes of processing, storing and sending orders as to the application and self-approval of these processes. The model has a good detail. |
Tonelli et al. (2016) | Specific model to improve operational performance through industry 4.0. | Santos and Martinho (2019) | The proposed maturity model is specifically targeted at industrial companies evaluating under five dimensions (strategy, structure and organizational culture; workforce; smart factories; smart processes; smart products and services). |
Ganzarain Epelde and Errasti Lozares (2016) | The model only provides concepts for diagnosing the company’s vision and assessing the use of enabling tools in industry 4.0, without any description of the processes. | Gajsek et al. (2019) | In this article a model is developed to assess the level of maturity of industry 4.0, however more directed to the levels of automation, in the production systems specifically of a steel company. |
De Carolis et al. (2017) | Specific model to enable industry 4.0 for manufacturing companies, missing documentation. | Werner-Lewandowska and Kosacka-Olejnik (2019) | The developed model aims to assess the maturity level of the technologies of industry 4.0 in the area of logistics in the service industry (eg: construction, transportation, |
Gökalp et al. (2017) | Model directed to application in the most strategic areas of companies such as: process transformation (for enabling technologies), data governance, asset management and organizational alignment areas.There is no detailing, at least in order to exemplify, of processes considered. | Facchini et al. (2020) | The framework for evaluating the concepts of industry 4.0 is presented, specifically, in the area of business logistics as well as developing a roadmap for the improvement process. |
Weber et al. (2017) | It consists of broadly demonstrating the application of Internet of Things (IoT) by means of criteria. | Lizarralde et al. (2020) | It is a model adapted to small and medium companies (SMEs) in the manufacture of Machine Tool companies (MT) that assesses the technologies of the industry 4.0 in |
Jæger and Halse (2017) | It consists in broadly demonstrating the evaluation of the application of the Internet of Things (IoT) by means of recommended criteria. | Shan et al. (2020) | In this work, an application model of the concepts of Industry 4.0 and Industrial Internet specifically in Heavy Industry. |
From the comparison of the analyzed models and the identification of opportunities for improvement between them, the model proposed in this research effort considers the application in the processes of a global company in the supply chain, not being restricted to industrial facilities or specific areas as the models analyzed, which includes from the beginning of the demand request, also industrial activities, until the post-sale analysis; finally, an unprecedented indicator was developed, as well as its calculation method, to measure the application level of industry 4.0 concepts in organizations according to the state-of-the-art in the evaluated processes.
3. Research Methodology
This work has a broad view on the influence of industry 4.0 in industrial enterprises maintaining competitiveness with sustainable growth in global markets increasingly demanding being one of the key levers for profitability.
Aligned with this concept, we understand that industry 4.0 involves integration with strategy, planning, development, implementation and operation, the latter with regard to direct users in the industry. This involves the strategic business vision with engineering, project management, production systems, supply chain, manufacturing, delivery, research and development, supplier development, sales, operation and after-sales and other actors that are not necessarily within internal companies’ borders.
The research procedure can be divided into four distinct phases. An initial phase creates a complete understanding of all the enterprise processes. The second stage refers to the model bases construction as well as the detailing of the global company process and the respective assessment form and results presentation. The third step is to carry out the evaluation by the experts in each process considered of the global supply chain company and, finally, the fourth and final stages correspond to indicators calculation and results presentation.
3.1. Enterprise process
As the enterprise referring to the case studied in a global company, all its processes were understood, when considering a manufacturing area, the starting point was demand generating and the end point is considered after sales.
The flow that represents all the steps is shown in Fig. 2, which shows that some processes are sequential and others started in parallel, the process design includes five macro-processes and these are unevenly distributed in 26 processes.

Fig. 2. Enterprise macro-process and its details.
The general diagram (Fig. 4) is subdivided into five macro-processes, namely: (1) Supply Chain, (2) Manufacturing, (3) Deliveries, (4) After sales and, (5) Research and Development (R&D), the latter interfaces with all areas. It is possible to check all the details that were made in each macro-process, except after-sales and R&D, due to the particularity of these areas, it was decided to investigate the main inputs, outputs and interfaces with other areas.
3.2. Model bases
As the subject of this research effort is multidisciplinary, as it involves several knowledge areas, the theoretical framework research provided the identification of the conceptual bases to be used that will permeate the entire work.
The recommended model is based on a structure with two evaluation perspectives, the first being designated by levels and the second evaluation perspective are the company areas called macro-processes, which in turn are divided into processes.
Levels are the conceptual references that guide the entire model (Table 2), so when developing the criteria for each process, they must necessarily meet these criteria, the scale used (1 to 4) is a reference to how management would be in the four industrial revolutions.
Level | Description |
---|---|
1.0 | The entire process of information, receipt, consolidation, decision-making and starting is documentary and carried out necessarily based on documents and through analysis “Face to Face” - F2F - being with another person or document. |
Industrial production system (without standardization). The entire information system is humanized (inputs, processing and decision making) | |
2.0 | Part of the information processing is automated as the receiving step, however consolidation is manual as well as the decision-making and triggering process, which also depend on manual input. |
Mass production, standardization and production system without flexibility. Telephony communication system, manual documentation, manual decision-making process | |
3.0 | Automation without integration. Automated system, however, decisions are made by the operator. It does not have the Intelligent Information System. |
Receiving and consolidating information automatically, but not integrated. Decision making dependent on manual input | |
4.0 | Flexibility and autonomy of the production systems, in an efficient, fast, intelligent and customized process, meeting more specifically the needs of customers in a competitive way. Fully integrated information systems. Decision making without manual influence. |
Completely autonomous and intelligent process based on the parameters and scenarios of the software (by means of physical and/or virtual robot): receipt, consolidation, decision making and triggering without manual influence and improvements established through machine learning. |
3.3. The model concept
In this phase, it corresponds to the criteria elaboration that define each company process used according to model bases defined in the previous phase.
To facilitate the different analysis of the industry 4.0 concepts application, the 26 processes are divided into 63 assessment items, as shown by the examples in Table 3.
Macro process | Exemplary of the items |
---|---|
1. Supply Chain | Customer Demand; Sales Master Plan (SMP); Production Master Plan (SMP); Bill of Material (BOM); Material Requirement Planning (MRP), Purchase Orders... |
2. Manufacturing | Wharehouse Picking; Manufacturing; Manufacturing Quality Control; Performance Test, Manufacturing Flexibility, Product Storage, Performance Machines,... |
3. Delivery | Customer Delivery; Delivery Accuracy, Wharehouse Picking; Product Traceability, Reverse Logistic, Life Cycle Product |
4. After Sales | Digitalization of sales/services, Mobile devices utilization; Costumer’s Digital media competence; Receiving customer information.... |
5. P&D | Governance; Customers Relationship, Innovation Process, Open Innovation development; interdepartmental collaboration,... |
Some processes are evaluated by more than one item, in this case, the arithmetic average of all items that make up the result of the evaluation process is considered.
As a next step, the criteria that define each application level in the processes considered were developed according to the bases (Table 2) that, as previously mentioned, permeate in the entire model, i.e., the levels which evaluate the 1.5.1 item named Purchase Order process is shown as follows (Fig. 3).
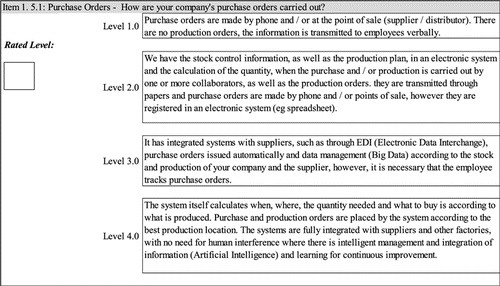
Fig. 3. Assessment checklist example.
The value that represents industry 4.0 application level in each macro-process, is represented by the arithmetic average of the processes that compose it, because it is understood that all have equal importance.
Then, the results achieved are represented by a radar chart where each vertex corresponds to each macro-process evaluated. Through this chart, the indicator called the industry 4.0 application index is calculated.
The indicator is calculated from the polygons area ratio, coming from the company evaluation under the model divided by the maximum possible area, in this situation when the enterprise reaches the maximum grade in all 63 assessment items. The index is evaluated between 0 (lowest possible value) and 100% (maximum possible value), finally a scale is presented which positions the company in relation to the defined state-of-the-art.
4. The Case-Study: Global Company
In this section, we present the model application based on a real case study in enterprise in the global high-tech supply chain in the capital goods sector. We chose an organization that already has applications in its various conceptual processes in industry 4.0, demonstrated by winning the digital transformation award in industry, smart logistics and other global innovation awards and has operation units, or a Research & Development center, in the five continents.
The company received a questionnaire and after explaining it started to fill it, which was carried out together with the application facilitator of the internal program in advanced manufacturing and experts in each macro-process, in this ensured knowledge in the environment of the internal processes as well in the industry 4.0 concepts; in the end, 21 specialists participated in this assessment process.
After the self-assessment, the answers were then inserted in the software tool to calculate application levels and create the report. In Fig. 4, it is possible to visualize the application level in each enterprise macro-process.
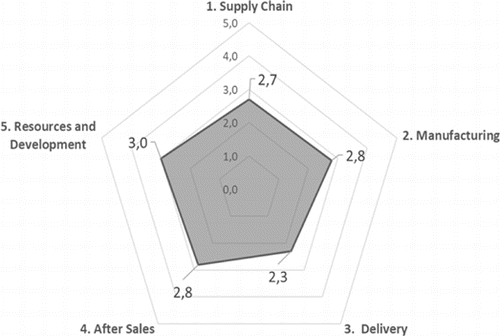
Fig. 4. Radar chart in the macro-process evaluated.
Figure 5 shows the details of the evaluated processes that compose the macro-process “Supply Chain”. It is noticed that the company that obtained the best score in the process was the material receipt (reached 3.2 out of 4.0) and the worst result was quality inspection (reached 2.0 out of 4.0).
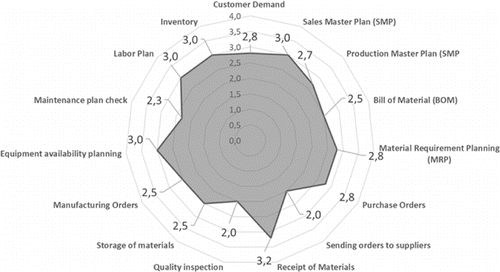
Fig. 5. Radar chart of the entire “supply chain” process.
For example, in Fig. 5, it is possible to see the item Production Master Plan (PMP) is evaluated by sub-items: (i) How the production schedule management is carried out (input data), (ii) How the production lead time is calculated and monitored and, (iii) How is product to product traceability for customer? The average rating of these three items reached 2.7 out of 4.0.
According to the result shown in Fig. 4, the industry 4.0 application index is calculated, based on the ratio between the areas of the formed polygons; hatched figure, which is the company assessment result divided by the maximum area formed, in this case, the company achieved the maximum score in all items (level 4).
Figure 6 shows the association between the proposed scale and its respective ranges, which are explained as follows:
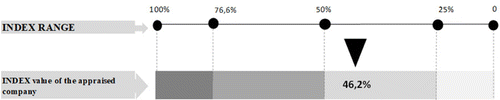
Fig. 6. Illustration of the company result evaluated in the Index scale.
• | Very Low Maturity: The company has the value up to 25% of the Index, for that the chart-built area after assessment done is equivalent to the regular pentagon area which levels is 2 in the five dimensions. This range represents that the enterprise has very low maturity in the industry 4.0 concepts according to the state-of-the-art defined. | ||||
• | Low Maturity: The company has the value between 25% and 50% of the Index, for that the chart-built area after assessment done is equivalent to the regular pentagon area between levels from 2.01 to 2.83 in the five dimensions. This range represents that the enterprise is in an attention situation regarding the industry 4.0 concepts according to state-of-the-art defined. | ||||
• | Relevant Maturity: The company has the value between 50% and 76.6% of the Index, for that the chart-built area after assessment done is equivalent to the regular pentagon area between levels from 2.84 to 3.5 in the five dimensions. This range represents that the enterprise has a significant maturity situation of industry 4.0 concepts according to the state-of-the-art defined. | ||||
• | High Maturity: The company has the value between 76.6% to 100% of the Index, for that the chart-built area after assessment done is equivalent to the regular pentagon area between levels from 3.51 to 4.0 in the five dimensions. This range represents that the enterprise is very close or already reached in terms of industry 4.0 maturity concepts according to state-of-the-art defined. |
5. Conclusion
This research work aimed to develop a model that systematically assesses the application of industry 4.0 concepts in the global supply chain enterprise.
In contrast to other approaches found in the literature, the main contribution of this research effort is to provide a model that specifically assesses the advanced manufacturing concepts in a global supply chain enterprise, not restricted to industrial facilities or specific areas, which included from the beginning of the demand request, also industrial activities, until the after-sales analysis based in five macro-processes and these are unevenly distributed in 26 processes resulting in 63 assessment items.
After conducting the assessment, the data collected from each macro-process are plotted on the Radar chart and from this graph the indicator that measures the application level of advanced industry concepts, described as industry 4.0 application index, it was developed in an unique way of measuring maturity through the area ration of the polygons after carrying out the assessment by the maximum possible area, that is, in this situation when the company reaches the maximum score in all sixty-three items.
The model transformation into a useful tool also allowed its easy application in practice. Early field experiences show that manufacturing enterprises are able to use the results of their self-assessment as a solid reference point for other strategic actions.
The results of the model proposed in this research effort, through the case study carried out, allowed a reflection on the strategies that the company has to address the state-of-the-art of the industry 4.0 concepts. This goes beyond evaluating its execution, or even evaluating isolated processes or proposing solutions without being aligned with the enterprises top management.
During the application and results analysis, it was found that companies do not necessarily intend to implement industry 4.0 in all their processes, due to budget, resource restrictions, or even a certain area is not a priority or because it does not have high economic potential in face of the investments and efforts required in the digital transformation that are required in hardware and software technologies.
Having said that, the proposed model allows for the gap identification for the company to carry out the analysis if at the moment evaluated they are identified as real opportunities for their business in order to prioritize the most relevant for each business.
The possibility of inserting the action plan in the evaluations carried out, associating it to each dimension, in this way, will make it possible to have all the information centralized, avoiding files and documents outside the tool and, finally, it was also understood as relevant when viewing your information in the radar chart that may also have available the result average of the other companies in the sector that represents the ecosystem in which it is inserted, to maintain the companies data confidentiality, whose objective is to make comparisons and assess existing gaps and improvement opportunities in relation to the sector average in which they operate.
Finally, new studies are suggested as a proposal to continue the knowledge evolution, so future research will focus on the application of the same assessment in other units around the world to provide data on the company’s best internal practices; it is also proposed to carry out a company assessment in the electronic components manufacturing sector, because according to the government it is the sector that has the most technology in its processes, which we will have references for other Brazilian industrial sectors.